June 10th 2025 - Accelerating chemical process & prodcution utilising Fast Batch reactor technology
Following a successful presentation by Ben Deadman at ChemUK 2025, PTSC are happy to announce that the presentation is available on demand!
Complete the form below to access the presentation
May 1st 2025 - Hydrolysis of Acetic Anhydride in a Fast-Batch Reactor Operating in Semi-Batch Mode
This third white paper in Dr. Benjamin Deadman’s series examines the PI QFlux® fast-batch reactor’s ability to control exothermic reactions under semi-batch conditions.
Building on previous findings, this study uses the hydrolysis of acetic anhydride to show how the PIQFlux®’s superior cooling enables tighter temperature control and 62% faster dosing compared to conventional systems.
The results highlight the reactor’s value in boosting efficiency and safety for challenging processes, paving the way for future work on selectivity and complex chemistries.
To View the White Paper fill in the Form below
April 15th 2025 - Performance of Heated Reactions in Fast-Batch Reactors
This second white paper in Dr. Benjamin Deadman’s series focuses on the performance of the PI QFlux® fast-batch reactor—a technology offering a major leap forward in thermal efficiency for batch processing.
Building on the first instalment, which highlighted the PI QFlux® reactor’s ability to heat faster than conventional systems, this paper explores how that thermal advantage translates into significantly reduced reaction times for bimolecular processes.
The results show where the PI QFlux® system delivers the greatest productivity gains and lays the groundwork for future studies on its impact in more complex and exothermic reactions.
To View the White Paper fill in the Form below
March 31st 2025 - Simulating Dynamic Thermal Conditions in Fast-Batch Reactors
Introducing the first in a series of white papers by Dr. Benjamin J. Deadman, focusing on the groundbreaking PI QFlux® system—a major advancement in fast-batch reactor technology. This installment highlights its superior thermal performance, which enhances productivity and selectivity in chemical processing.
To support this innovation, ReactorPy, a Python-based modeling tool, has been developed to simulate dynamic thermal conditions, enabling precise control and optimization of reactor performance.
Future papers will delve deeper into reaction kinetics and volume modifications, further unlocking the full potential of the PI QFlux® system.
Dr. Benjamin Deadman
Ben has over 15 years of experience in the application and development of enabling technologies for the study of chemical reaction processes.
Specialising in:
- High-Throughput Experimentation (HTE)
- Flow Chemistry
- Reaction Analysis
- Design of Experiments (DOE) for chemistry research
To View the White Paper fill in the Form below
December 3rd 2024 - Heat transfer society webinar presentation
Following a successful webinar in collaboration with the Heat transfer society, PTSC are happy to announce that the presentation is available to view on demand!
Complete the form below to access the presentation
October 28th 2024 - Heat Transfer Society webinar announcement
PTSC and Heat Transfer Society to Host Webinar on Revolutionary PI Qflux Reactor Technology for Chemical Batch Reactors - 29th November 12:00 GMT
PTSC is excited to announce an upcoming webinar, presented in collaboration with the Heat Transfer Society, to introduce the breakthrough PI QFlux reactor technology. This event will highlight how this state-of-the-art solution can deliver an impressive 300% increase in heat transfer efficiency and productivity in chemical batch reactors.
Webinar highlights will include:
Enhanced Heat Transfer Mechanisms: Discover the advanced technology behind the PI Qflux reactor and how it achieves unprecedented heat transfer rates.
Broad Industry Applications: Explore the potential applications across various sectors aiming to boost both efficiency and sustainability.
Join us to see how PI Qflux can elevate productivity and innovation in your industry.
Sign up to the webinar on the Heat transfer society’s website below:
August 12th 2024 - Advances in Chemical Manufacturing: PTSC and Kobelco Eco Solutions Partnership
We are excited to announce that PTSC has finalized a manufacturing supply agreement with Kobelco Eco Solutions Co.,Ltd Japan for the groundbreaking PI QFlux batch reactor.
This collaboration marks a significant milestone in driving innovation within the chemical manufacturing sector, setting the stage for revolutionary advancements in process technology & sustainability.
April 9th 2024 - PTSC granted European Patent for PI QFlux
Another milestone achieved! Our PI QFlux chemical batch reactor has been granted a European patent, adding to our existing US and Indian patents, as well as pending filings in Japan and China. This is a validation of the technology's uniqueness and its "World's most productive batch reactor" title.
March 22nd 2024
Following the successful live webinar in Collaboration with De Dietrich Process systems North America, PTSC is happy to announce that the webinar is now available to watch on demand.
Complete the form below for access to the presentation:
March 1st 2024
The chemical industry has utilized the same, traditional batch reactor technology for decades, with minimal advancements made to most processes during this time period. Learn how the new “optimized throughput” batch reactor technology can massively benefit productivity, quality and energy efficiency at production scale, especially within the fine and specialty chemical segments.
What will you learn?
Overturning long held assumptions on the capabilities possible with batch reactor production systems.
Who should attend this webinar?
Anyone who has an interest in learning about the substantial improvement to their chemistry output possible through technology changes from that of traditional batch reactors; without having to transition to radical process change such as Flow Chemistry.
December 2023 - De Dietrich Process Systems and PTSC Announce the Launch of the Revolutionary PI QFlux Batch Reactor System in North America
PTSC is pleased to announce the signing of a Memorandum of Understanding (MOU) with DDPS US, as both parties develop the new licensing agreement for the marketing, distribution and manufacture of PTSC’s revolutionary PI QFlux batch reactor system for the North American markets.
PTSC holds patents for the PI Qflux fast batch reactor technology in the US and will continue to retain all IP and technology ownership under the arrangements.
DDPS US’ extensive capabilities in systems design and integration combined with their manufacturing expertise will be married with PTSC’s design and innovation in batch reactor and thermal fluid control packages to provide locally based advance batch reactor system technology.
"We are thrilled to bring the PI QFlux batch reactor system to North American businesses and industries. This product is a testament to our joint commitment to innovation, sustainability and efficiency, and we believe it will be a game-changer in chemical and pharmaceutical applications," said Don Doell, CEO at DDPS US.
The groundbreaking design of the PI QFlux batch reactor systems features up to five times higher heat transfer performance and 50% energy savings over conventional batch reactors, representing a significant leap forward in productivity optimization.
Andrew Wills, Managing Director and Founder of PTSC, commented, “The PI QFlux batch reactors’ exceptional and precise heat flux enables a vastly superior batch controllability and bulk scalability. With up to four times the throughput in terms of STY (Space Time Yield), the PI QFlux shorter controlled batch cycles positively impact the performance of the chemistry product quality and yield.”
November 2022 - “This batch reactor saves time, energy, space and more” - Thank you to Chemical Engineering Online for doing another feature on the PI QFlux Reactor
https://chemengonline.com/batch-reactor/
Download the full November issue of Chemical Engineering Online here: https://chemengonline.com/issues/2022-11
October 2022 - Thank you to Heat Exchanger World Magazine for doing a deep dive into the PI QFlux in their October Edition
Heat Exchanger World - here
Or use the link to download the pdf, or see the full article below
September 2022 - US Patent Office Issues PTSC a Patent for the PI QFlux Reactor
PTSC Ltd has had the patent for the PI QFlux Reactor issued by the US Patent Office
Patents have also been applied in Europe, India, China and Japan
In order to achieve a heat flux of 4 times greater than conventional glass lined reactors, the PI QFlux has many innovative features which range from incremental to radical, therefore, having these technologies protected via patents marks a major milestone in the development of the PI QFlux Reactor
July 2022 - PI QFlux Industrial Scale Performance Testing Complete
PTSC has carried out extensive testing of its PI QFlux batch reactor vs an equivalent sized industry traditional batch reactor. Both reactors were constructed in glass lined steel and both operated with the same service connections.
Within one day of testing starting and continuously afterwards, the PI QFlux faultless achieved a heating/cooling rate 4 times higher than that of the conventional reactor due to both the unique design of the PI QFlux reactor and its PTSC/TFS designed TCU. Importantly and in combination, the unique design of the PI QFlux resulted in up to 50% reduction in primary heat energy consumption over that of the conventional reactor, whilst performing this feat.
PTSC who provided the PI QFlux technology as well as the new design of TCU were greatly supported in the test by Kobelco Eco Solutions Japan, who constructed the test centre and provided all of the process infrastructure required to carry out such a large full scale production trial.
May 2022 - PTSC introduces the benefits of the PI QFlux revolutionary batch reactor concept.
PTSC will be joining our sister compay Thermal Fluid Systems Ltd on their stand at CHEMUK2022.
September 2021
PTSC and Kobelco Eco Solutions Co Ltd of Japan are currently collaborating on the first full scale trials of the new PI Reactor and Single Phase Parallel Flux TCU developed by PTSC and protected under global patent approval.
This next generation batch reactor will massively increase the productivity and performance of both Alloy and Glassed Lined Reactors as well as reducing energy consumption in operation. The fully scale performance trials will be carried out at a purpose built test centre currently under construction near Kobe, Japan where the PI Reactor and TCU will be performance matched against a same volume traditional batch reactor in the first half of 2022.
September 2021
August 2021
Thermal Fluid Systems Ltd, specialists in the design and provision of thermal fluid control systems, announced that under a change of shareholder ownership it would now become a full affiliate company of PTSC, as a result of both companies ultimate shareholding.
Thermal Fluid Systems Ltd are the UK’s undisputed leader in the design, manufacture and installation of single fluid thermal control packages, with over 35 years of experience and some +500 installations.
The vast international and local client list of Thermal Fluid Systems Ltd along with its unique proven design IP data base will enable the future developments being undertaken by both PTSC and Thermal Fluid Systems Ltd, in our efforts to decarbonise the chemical and industrial sectors.
Details of Thermal Fluid Systems can be found at www.thermalfluidsystems.co.uk
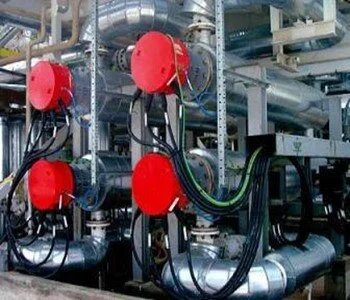
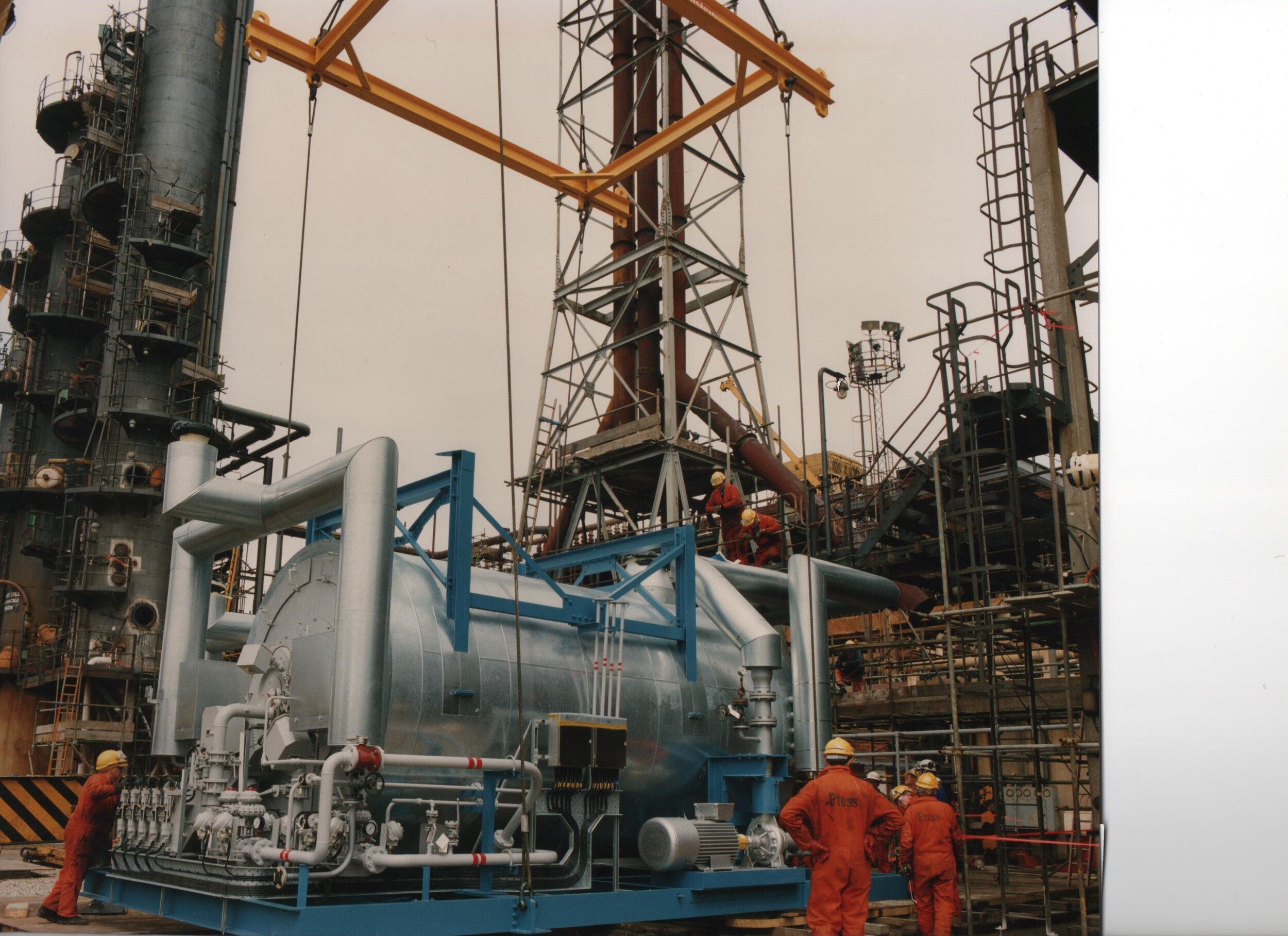
January 2021
PTSC has entered into an agreement with Apaco AG - Swiss made energy systems, including the former team of Bertrams Heatec to support the current installed base of equipment in the UK and Ireland as part of the established long running agreements that were in place between Bertams Heatec and Thermal Fluid Systems Ltd.
Capacity: 3 x 10’500KW
Efficiency: 92.5%
HTM: Water/Glycol
Design Pressure: 16.7 bar g
Design Temperature: 110°C
Fuel: Natural Gas (1’074Nm3/h per heater)
Capacity: 2 x 3’755KW
Efficiency: 92.5%
HTM: Regeneration Gas
Design Pressure: 225.5 bar g
Design Temperature: 225°C
Fuel: Natural Gas (385Nm3/h per heater)
Capacity: 3 x 10’250KW
Efficiency: 95.24%
HTM: Water/Glycol
Design Pressure: 25 bar g
Design Temperature: 150°C
Fuel: Natural Gas (989Nm3/h per heater)